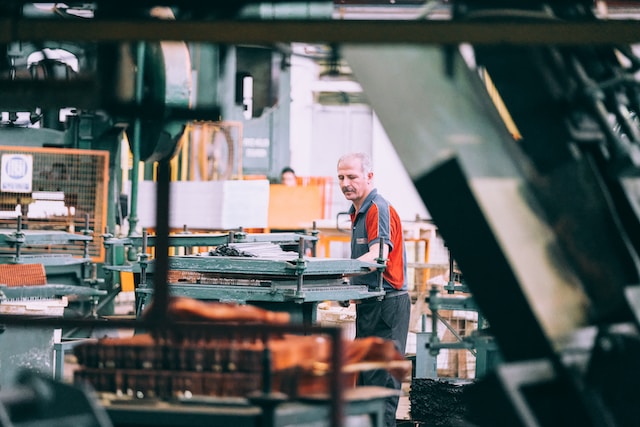
Understanding Injection Molds Before You Start Your Project
A plastic injection mold cannot be changed after it’s been fabricated, which makes the planning and design process a crucial first step for every new project. Fasteners can be added to injection-molded parts by either modeling threads directly on the part or including pre-molded screws or threaded inserts. These can be modeled as “bosses” that protrude to allow for easy attachment.
What is an Injection Mold?
The injection molding process involves heated, melted thermoplastic polymers mechanically forced into molds in a high-pressure environment to create the desired final products. It’s a highly versatile process that industries use to produce everything from toys and medical devices to automotive parts, packaging, and more. Injection-molded plastic is commonly used in the pharmaceutical industry to manufacture multipurpose products such as plastic syringes. Test tubes, beakers, housings, and equipment casings are sterile disposable instruments. In addition, injection-molded plastic is widely used for medical packaging and bottles. Injection-molded plastic is also used for many machinery and automotive parts, including dashboards, bumpers, radio controls, cup holders, and car doors. This type of plastic is valued for its durability, resistance to weather and corrosive elements, and lightweight composition that helps contribute to vehicle fuel efficiency. Injection molded parts are typically made of plastics such as HDPE, PP, PET, nylon, and PBT.
What is the Process of Injection Molding?
The plastic injection mold makers produce parts made of plastic or elastomeric material. The process involves inserting molten plastic into the tool and cooling it to solidify the product. Highly experienced machinists produce tools from materials like steel or aluminum that can survive the high heat and pressure of the injection machine.
Mass manufacturing is excellent for injection molding because of its extremely high output rate. The sprues and runners – the plastic that gets wasted due to the injection channels – can be reground and recycled for future use. Injection-molded products are everywhere, from plastic containers to household items like hangers and shower curtains. It is also commonly used to create medical devices, such as blood pressure cuffs and stethoscopes. It is also famous for creating sporting goods, toys, and tools.
What is the Size of Injection Molding?
Many products are manufactured using injection molding, including wire spools, toys, bottle caps, combs, and musical instruments (and their components). Injection molding offers high precision and is ideal for mass-production applications. Injection molded parts are usually made with polymers, sometimes called resins. A wide range of resins is available, each with different properties. Each resin has a specific melt point, which should match the final part’s requirements. Most plastic injection machines are limited in how large a single piece they can mold. Because of this, it’s crucial to design your product for manufacturing with few undercuts and changes in wall thickness. It will help reduce costs as the complexity of the mold increases with each variation. A further strategy to reduce costs is to avoid pricy high-grade finishes. Instead, add embossed text to your design for logos, warnings, diagrams, or instructions.
What is the Material of Injection Molding?
Injection molding may be done with many different kinds of plastic. The resin chosen depends on the product design and its requirements. For example, designs for bendable sections or living hinges require flexible plastic like polypropylene. Structural parts that withstand harsh environments can be made from more durable plastics such as polycarbonate or nylon. The choice of fillers is also essential. Eco-fillers, such as soft recycled glass fibers and structural lignocellulosic fibers from wheat straw, can be added to enhance the performance of injection-molded parts.
Injection molding is an excellent manufacturing technique for complex products. However, the cost of creating an injection mold is a significant hurdle to overcome for low-volume production runs. For this reason, minimizing part size and the complexity of a design are critical factors in keeping costs down. Injection molds can be made from metals such as aluminum and steel or thermoplastics. Single or numerous cavities can be found in injection molds. Each cavity can contain identical parts or can be unique to allow for the formation of different geometries.