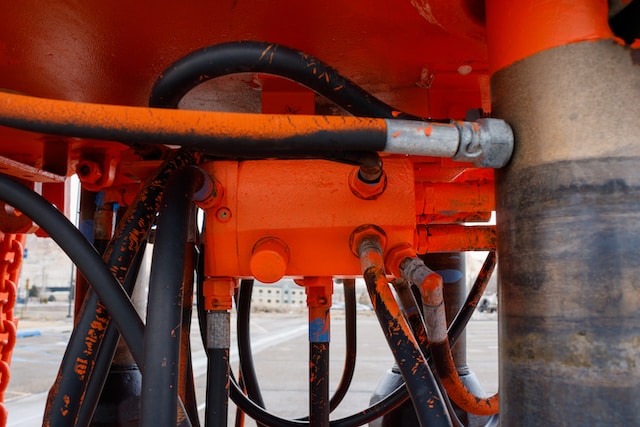
Protecting Your Parker Hoses From Damage
Hoses may make up only a small part of your equipment and machinery, but they can be the source of big problems and serious injuries. Your local ParkerStore can help you protect your hoses from damage with a wide selection of protective solutions. Inspecting components before assembly should include checking for blisters, loose covers, kinks or cracks.
Inspection
Regular inspection of Parker Hose & fitting inventory Charlotte, NC, is crucial for ensuring the safety and reliability of hydraulic systems. Hoses and fittings are subjected to various operational stresses and conditions, leading to wear, tear, and damage. These defects can cause leaks, malfunctions, and even catastrophic failures. A thorough inspection should involve visually examining each hose and fitting and checking for leaks and proper fit. Hoses should be inspected for cracks, abrasions, bulges, and other signs of damage. Fittings should be inspected for loose connections, corrosion, and wear. In addition to visual inspection, it should also be subjected to pressure testing. This will help identify weaknesses or leaks that may not be visible to the naked eye. Pressure testing should be performed by a qualified technician using the appropriate equipment. By following these guidelines, you can help ensure that your Parker Hose & fitting inventory is in good working condition and that your hydraulic systems operate safely and reliably.
Maintenance
Keeping your hoses in peak condition requires a proactive approach. Achieving maximum hose life requires attention to installation, routing and maintenance. It is important to ensure the system is pressurized and free of air entrapment before use. This should be done daily to avoid leaks, kinking and flow restriction. It is recommended to follow the system manufacturer’s instructions regarding chemical resistance and, if necessary, perform compatibility testing at elevated temperatures. Routing should be designed to prevent inherent problems (kinking, flow restriction, bending smaller than the minimum bend radius and proximity to hot surfaces). The hose assembly should be routed fail-safe so that escaping media does not endanger personnel or damage property.
Replacement
Hoses are often exposed to harsh environments and extreme conditions that can damage the hose and cause premature failure. Sometimes, the results of these adverse conditions are visible to the naked eye (excessive abrasion on the outside hose cover, cracking or hardening of the hose cover, kinking in the hose or deterioration of the inner tube) while other times it is not. When a hydraulic hose fails, it can cause serious injury and expensive downtime. Preventative maintenance schedules, knowing how to recognize hose wear and having the correct hose replacement on hand can reduce unscheduled downtime and help your business thrive.
Testing
Testing is essential in ensuring that the hose assembly is safe and ready for use. This test is performed by bringing the hose to a minimum pressure and then gradually increasing the pressure to the desired rated pressure while inspecting for leaks, bulging, or coupling slippage. The hose must be completely free of air bubbles for the entire duration of this test to ensure safety. This is done by capturing one end of the hose with a cap or plug and then filling it up with water or another liquid that can be used as a test medium. Leaking is often indicated by the appearance of water droplets emitted from multiple locations within the hose. A more severe test is the flex impulse test, which involves subjecting the hose to several pulses (very short, sharp pressure peaks) while bent in tight bends. This testing is designed to simulate the flexing applications most hoses are subjected to and can quickly sort out the good hose assemblies from the bad.